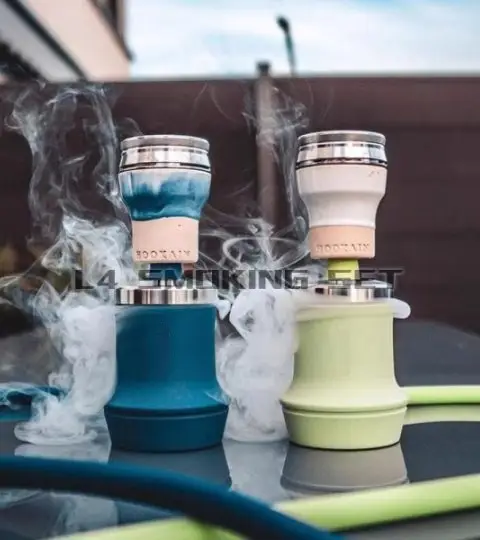
We met this project at the end of 2020, a customer selling hookah asked if we could make plastic molded with soft surfaces, we called this effect silicone oil spraying.
We sent samples with silicone oil spraying for the customer’s confirmation and received their initial design. Identifying impractical elements like excessive thickness and heavy metal parts unsuitable for injection molding, we faced initial resistance to change. Undeterred, we collaborated to enhance the design, aligning with their philosophy, product assembly, and usage environment. Since 2020, we’ve iterated on CNC prototypes to continually refine the product.
Finally, in March 2021, the customer wholeheartedly endorsed the design. This marked the initiation of mold production for the complete sets. The product takes the market by storm, selling very well and leaving a lasting imprint on the success chart.
The three on the left are the base part of the product, a plastic piece over-molding stainless steel part. The red part on the far right is the body. We originally considered the two parts of ultrasonic welding to achieve the waterproof effect. Because the base was too heavy, the main body and the base part were broken during the transportation process, so we communicated with the customer to change the design to a screw locking scheme and added a silicone gasket on the base to achieve a waterproof effect.
The processes involved in this project include plastic over-molding metal parts, soft plastic over-molding hard plastic, screw assembly, hardware, and other accessories assembly, surface spray primer and silicone oil, LOGO silk screen, etc. Because the product was very successful, the customer was very satisfied and finally decided to put the production of assembly and packaging on our side for processing.
Finished product show
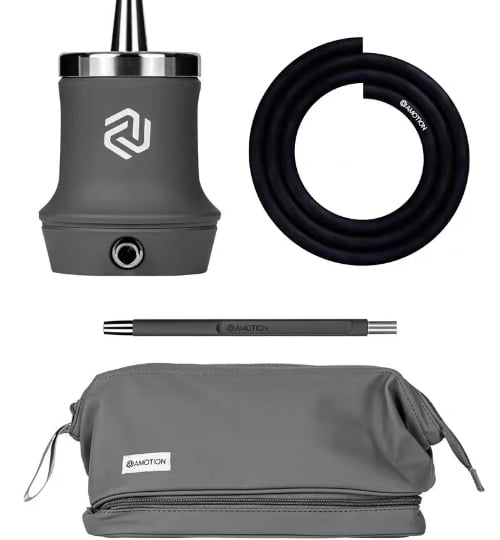
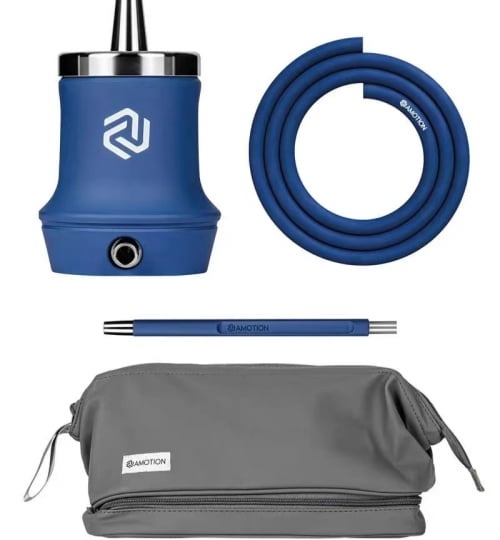
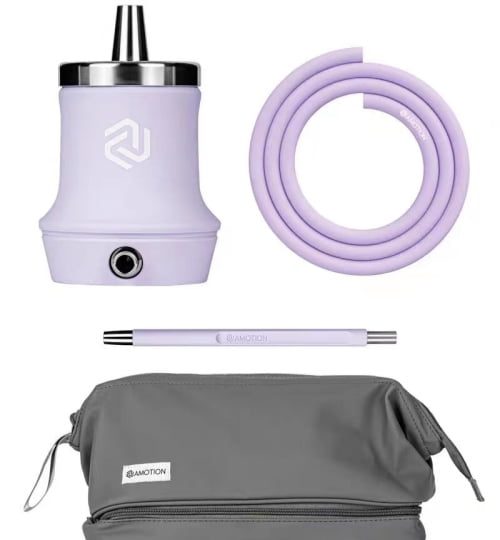
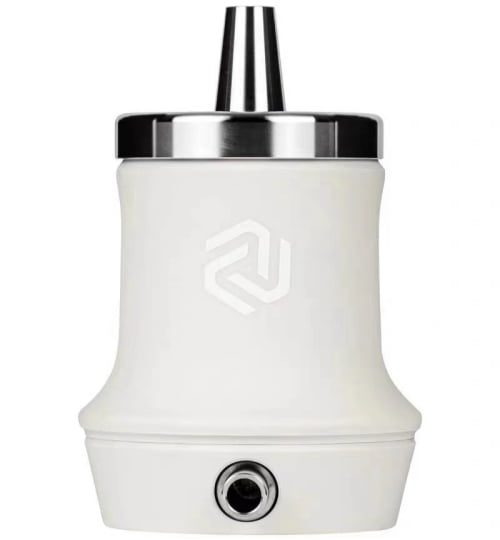
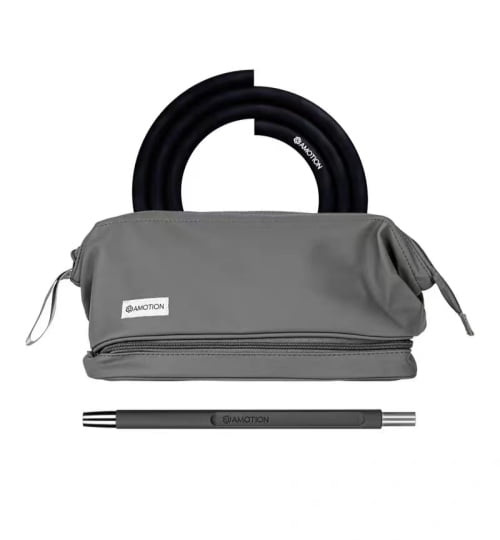
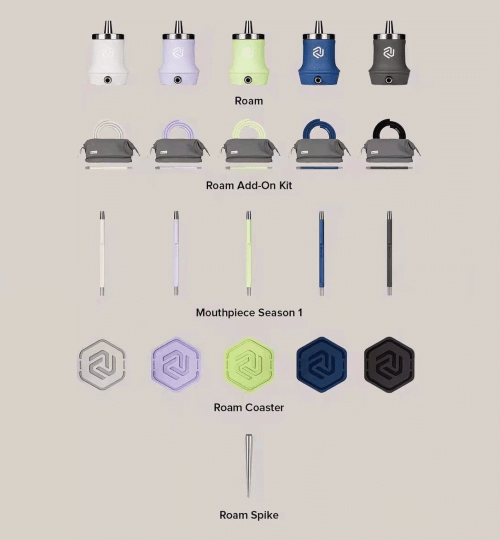
Click below picture to see the production and assembly.
Bring your product idea to life in as soon as 5 days!
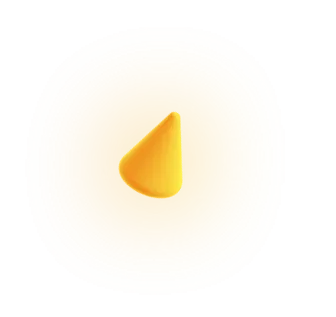
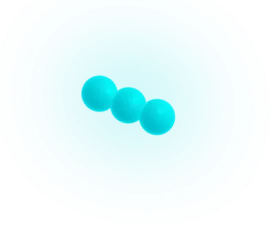